Fractures in nuclear graphite
Collaboration with EDF Energy and Jacobs/Amentum
UK Nuclear Power Plant Safety
The team that founded Mesh-Oriented Solutions worked together successfully on developing MoFEM to meet the needs of the UK nuclear industry—EDF Energy and Jacobs/Amentum. The work focused on providing simulation capabilities to predict fracture in the cores of UK nuclear power plants. MoFEM delivered an advanced crack propagation simulation tool that predicted fractures far more accurately than any commercial or open-source code. EDF Energy commissioned two independent audits of MoFEM, in 2017 and 2019. Based on these, MoFEM was approved for use in safety cases supporting the continued operation of UK nuclear power plants. Since then, MoFEM has been used consistently by engineers at EDF Energy and Jacobs/Amentum. The work resulted in:
-
Impact on Nuclear Safety: Facilitating the use of novel technology for simulations supporting safety cases for the UK’s
nuclear power plants
operations, thanks to sustainable development practices within the MoFEM team. -
REF2021 Impact Case Submission: Submitting an impact case to
REF2021
, demonstrating significant cross-disciplinary applications of the research.
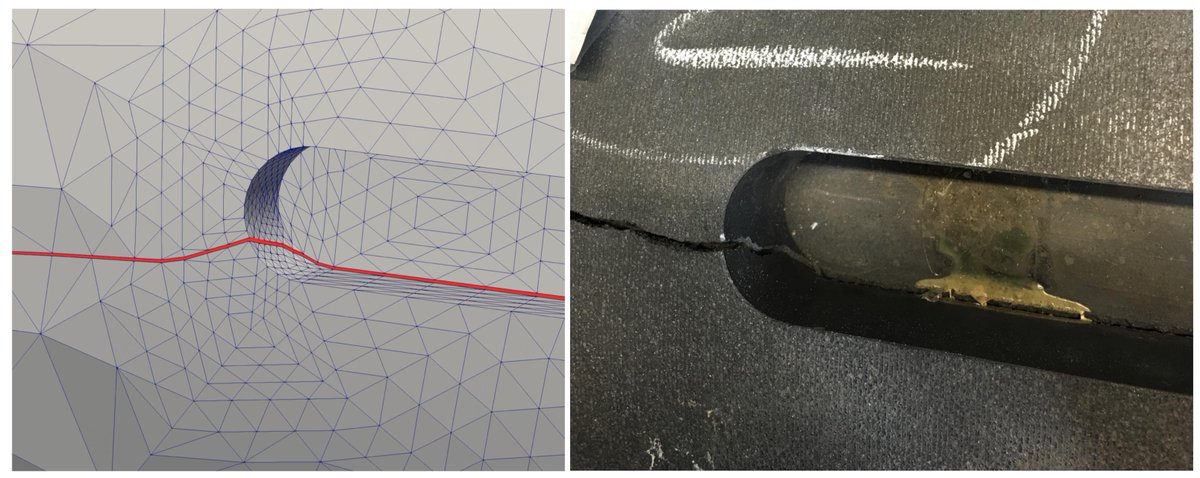
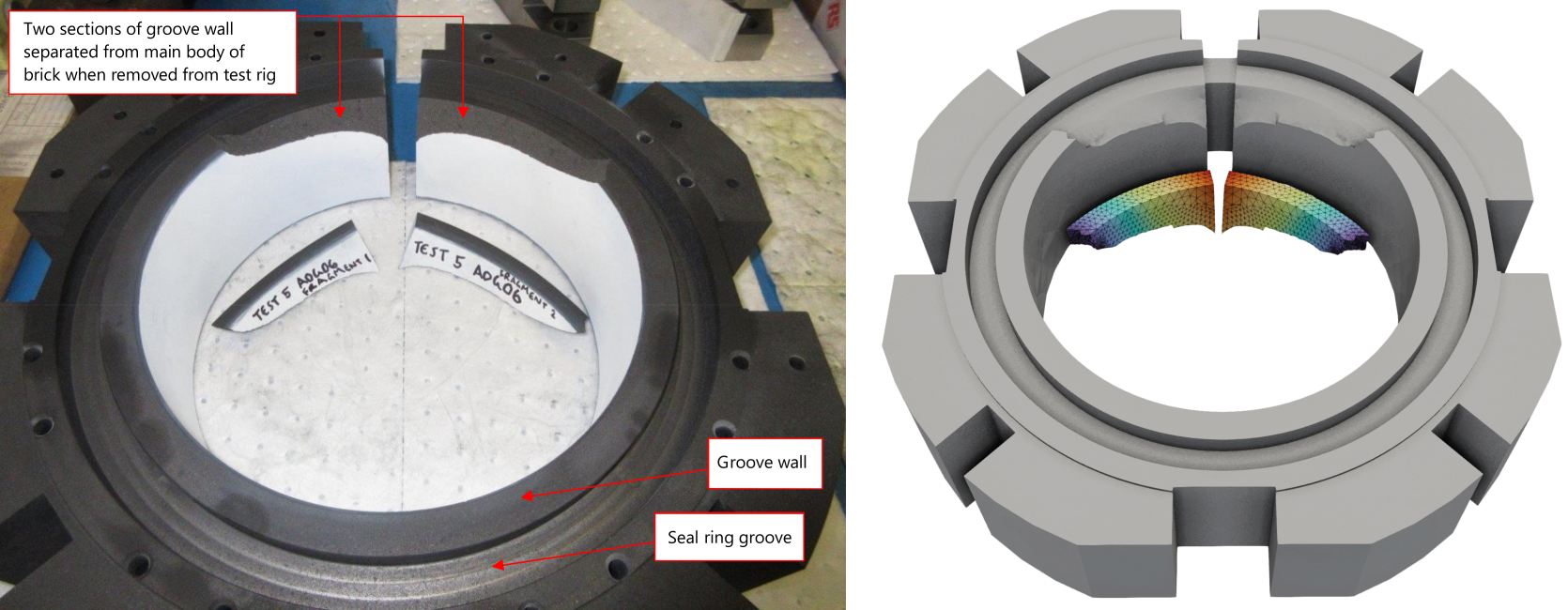
Configurational Mechanics in Heterogeneous Materials
Accuracy and robustness of crack propagation in nuclear graphite were achieved by implementing a novel computational framework in MoFEM,
“Configurational Mechanics for Modelling Continuous Crack Propagation in Heterogeneous Materials” which extends the principles of configurational mechanics
to modelling crack propagation
in brittle
, heterogeneous materials
. Key aspects of this work include:
-
Theoretical Basis: Utilizing principles of
configurational mechanics
, based on the local form of thefirst law of thermodynamics
, for establishing equilibrium conditions for thecrack front
. -
Crack Propagation Direction: Applying the principle of
maximal energy dissipation
to determine the direction of crack propagation in line withconfigurational forces
. -
Handling Heterogeneous Materials: Extending previous formulations to include the influence of
spatially varying material stiffness
, introducing an additional force influencing the crack front movement. -
Monolithic Solution Strategy: Simultaneously solving for
material
andspatial displacements
, enabling discrete displacement discontinuity resolution without the need formesh refinement
orenrichment techniques
. -
Advanced Numerical Techniques: Implementing
arc-length procedures
for dissipative loading path tracing andmesh smoothing
for maintaining mesh quality. -
Demonstration of Efficacy: Validating the performance of this formulation through numerous
numerical simulations
, showcasing both accuracy and robustness.
This research marks a significant contribution to both the fields of engineering mechanics
and nuclear safety
, demonstrating the versatility and impact of the methodologies developed in MoFEM.